Die voordele van magnesia-koolstofstene is:weerstand teen slak-erosie en goeie termiese skokweerstand. In die verlede was die nadeel van MgO-Cr2O3-stene en dolomietstene dat hulle slakkomponente geabsorbeer het, wat gelei het tot strukturele afskilfering, wat tot voortydige skade gelei het. Deur grafiet by te voeg, het magnesia-koolstofstene hierdie tekortkoming uitgeskakel. Die kenmerk daarvan is dat die slak slegs in die werkoppervlak binnedring, sodat die reaksielaag beperk is tot die werkoppervlak, die struktuur minder afskilfering en 'n lang lewensduur het.
Nou, benewens tradisionele asfalt- en harsgebonde magnesia-koolstofstene (insluitend gebakte olie-geïmpregneerde magnesia-stene),Die magnesia-koolstofstene wat op die mark verkoop word, sluit in:
(1) Magnesia-koolstofstene gemaak van magnesia wat 96% ~ 97% MgO en 94% ~ 95% C grafiet bevat;
(2) Magnesia-koolstofstene gemaak van magnesia wat 97,5% ~ 98,5% MgO en 96% ~ 97% C bevat;
(3) Magnesia-koolstofstene gemaak van magnesia wat 98,5%~99% MgO en 98%~C grafiet bevat.
Volgens die koolstofinhoud word magnesia-koolstofstene verdeel in:
(I) Olie-geïmpregneerde magnesia-stene (koolstofinhoud minder as 2%);
(2) Koolstofgebonde magnesia-stene (koolstofinhoud minder as 7%);
(3) Sintetiese harsgebonde magnesia-koolstofstene (koolstofinhoud is 8%~20%, tot 25% in 'n paar gevalle). Antioksidante word dikwels by asfalt/harsgebonde magnesia-koolstofstene gevoeg (koolstofinhoud is 8% tot 20%).
Magnesia-koolstofstene word vervaardig deur hoë-suiwerheid MgO-sand met skubberige grafiet, koolstofswart, ens. te kombineer. Die vervaardigingsproses sluit die volgende prosesse in: rou materiaal vergruis, sifting, gradering, meng volgens materiaalformule-ontwerp en produksetprestasie, volgens die kombinasie. Die temperatuur van die middeltipe word verhoog tot naby 100 ~ 200 ℃, en dit word saam met die bindmiddel geknie om die sogenaamde MgO-C-modder (groen liggaamsmengsel) te verkry. Die MgO-C-moddermateriaal word met behulp van sintetiese hars (hoofsaaklik fenolhars) in 'n koue toestand gegiet; die MgO-C-moddermateriaal gekombineer met asfalt (verhit tot 'n vloeibare toestand) word in 'n warm toestand (teen ongeveer 100 °C) gegiet. Volgens die bondelgrootte en prestasievereistes van MgO-C-produkte kan vakuumvibrasietoerusting, kompressiegiettoerusting, ekstruders, isostatiese perse, warm perse, verhittingstoerusting en ramtoerusting gebruik word om MgO-C-moddermateriaal tot die ideale vorm te verwerk. Die gevormde MgO-C-liggaam word in 'n oond by 700~1200°C geplaas vir hittebehandeling om die bindmiddel in koolstof om te skakel (hierdie proses word karbonisering genoem). Om die digtheid van magnesia-koolstofstene te verhoog en die binding te versterk, kan vulstowwe soortgelyk aan bindmiddels ook gebruik word om die stene te impregneer.
Deesdae word sintetiese hars (veral fenolhars) meestal as die bindmiddel van magnesia-koolstofstene gebruik.Die gebruik van sintetiese harsgebonde magnesia-koolstofstene het die volgende basiese voordele:
(1) Omgewingsaspekte laat die verwerking en produksie van hierdie produkte toe;
(2) Die proses om produkte onder koue mengtoestande te vervaardig, bespaar energie;
(3) Die produk kan onder nie-uithardende toestande verwerk word;
(4) In vergelyking met teerasfaltbindmiddel, is daar geen plastiese fase nie;
(5) Verhoogde koolstofinhoud (meer grafiet of bitumineuse steenkool) kan slytasieweerstand en slakweerstand verbeter.
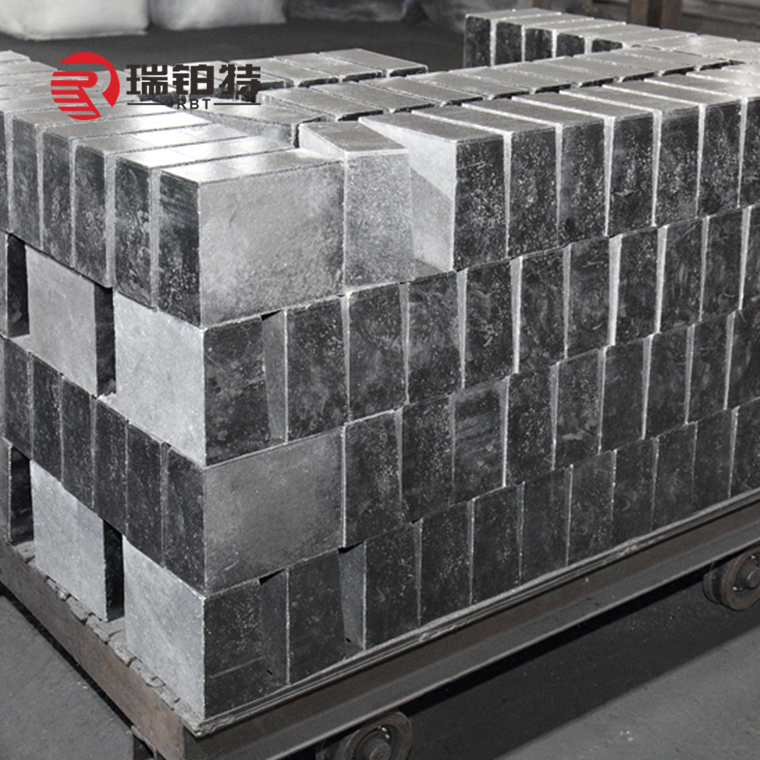
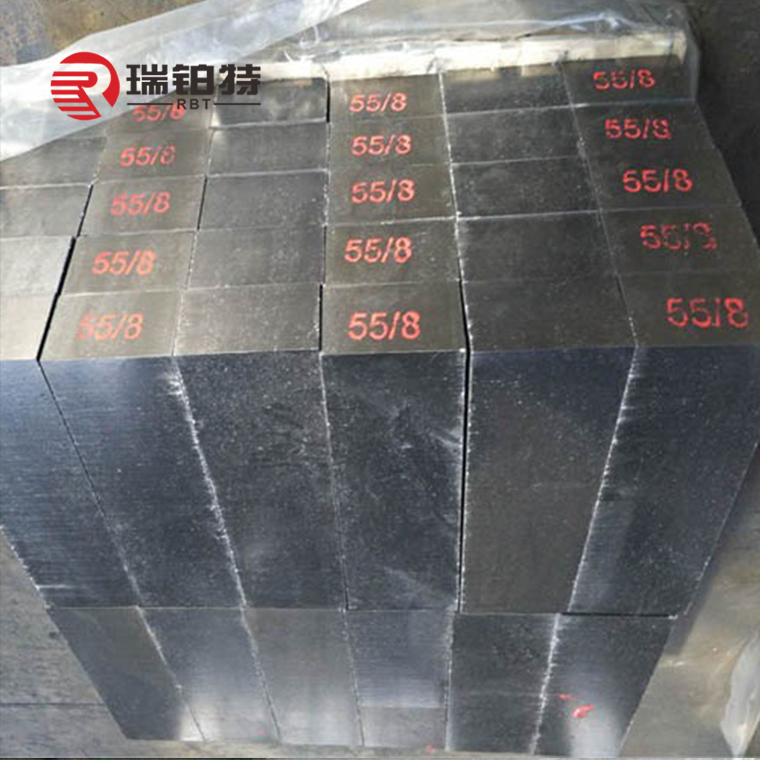
Plasingstyd: 23 Februarie 2024